Introduction:
In today's rapidly evolving industrial landscape, control cables play a crucial role in ensuring the smooth and efficient operation of machinery and equipment. These cables transmit signals and power to control various processes, making them an integral part of automation and control systems. To ensure optimal performance, safety, and interoperability, control cable standards have been developed and implemented. This article explores the importance of control cable standards, their key features, and their impact on industrial applications.
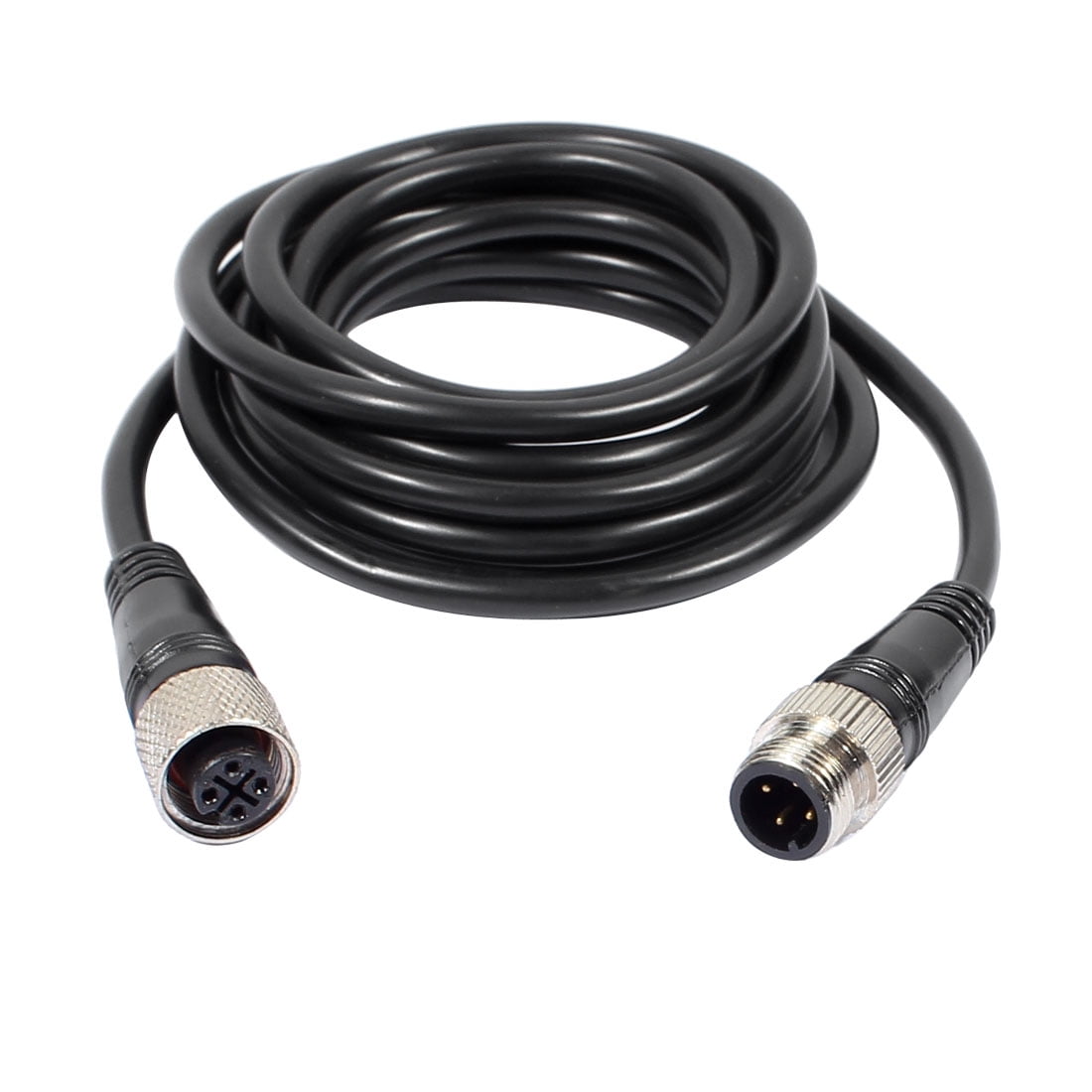
1. Understanding Control Cable Standards:
Control cable standards are a set of guidelines and specifications that define the design, construction, and performance requirements for cables used in control systems. These standards are developed and maintained by reputable organizations, such as the International Electrotechnical Commission (IEC) and the American National Standards Institute (ANSI), in collaboration with industry experts, manufacturers, and users.
2. Importance of Control Cable Standards:
2.1. MI cable protection levels and Reliability:
Control cable standards prioritize the safety and reliability of cables used in industrial applications. https://www.jiangyuancables.com/pvc-insulated-sheathed-power-cable/ specify requirements for insulation, shielding, and conductive materials, ensuring that the cables are resistant to electrical and mechanical stresses. By adhering to these standards, manufacturers can provide cables that minimize the risk of electrical hazards, such as short circuits or fires, thereby enhancing workplace safety.
2.2. Interoperability:
Standardization of control cables enables interoperability between different systems and components. By following a common set of standards, manufacturers can ensure that their cables can be seamlessly integrated into various control systems. This promotes compatibility, simplifies installation and maintenance processes, and allows for easy replacement or upgrading of cables without disrupting the overall system functionality.
2.3. Performance Optimization:
Control cable standards also focus on enhancing the performance of cables in industrial environments. They define requirements for cable flexibility, temperature resistance, and resistance to chemical and environmental factors. Compliance with these standards ensures that control cables can withstand harsh operating conditions, such as extreme temperatures, moisture, oil, or corrosive substances, without compromising their performance or lifespan.
3. Key Features of Control Cable Standards:
3.1. Cable Design and Construction:
Control cable standards outline specific design and construction requirements to ensure optimal performance. They define parameters such as the number and arrangement of conductors, insulation and jacket materials, and overall cable dimensions. These specifications help manufacturers create cables that can efficiently transmit control signals and power, while also providing protection against external influences.
3.2. Electrical and Mechanical Performance:
Control cable standards provide guidelines for electrical and mechanical performance characteristics. These include parameters such as voltage rating, current-carrying capacity, impedance, capacitance, and bending radius. Manufacturers must meet these requirements to guarantee that their cables can handle the expected electrical loads and mechanical stresses, ensuring reliable operation over the cable's lifespan.
3.3. Shielding and Grounding:
To minimize interference and ensure signal integrity, control cable standards often include provisions for shielding and grounding. Shielding materials, such as foil or braided wire, are specified to protect against electromagnetic interference (EMI) and radio frequency interference (RFI). Proper grounding techniques, as defined by the standards, help eliminate unwanted electrical noise and maintain signal quality.
3.4. Fire Resistance and Flame Retardancy:
Due to the potential risks associated with fire incidents, control cable standards often include requirements for fire resistance and flame retardancy. PV cable lifespan define tests and criteria that cables must pass to ensure their ability to withstand fire and limit the spread of flames. By adhering to these standards, manufacturers can offer cables that contribute to overall fire safety in industrial environments.
4. Impact of Control Cable Standards on Industrial Applications:
4.1. Automation and Control Systems:
Control cable standards play a crucial role in ensuring the effective functioning of automation and control systems. By providing guidelines for cable performance and compatibility, these standards enable seamless integration of control cables into complex systems, improving their reliability, efficiency, and overall performance.
4.2. Industrial Machinery and Equipment:
Control cable standards have a significant impact on the operation of industrial machinery and equipment. By complying with these standards, manufacturers can produce cables that withstand demanding conditions, reduce the risk of failures, and optimize the performance of critical control systems. This, in turn, enhances the overall productivity and efficiency of industrial processes.
4.3. Workplace Safety:
Adherence to control cable standards greatly contributes to workplace safety. By specifying requirements for insulation, shielding, and fire resistance, these standards help prevent electrical accidents and minimize the risk of fire incidents. Compliance with these standards ensures that cables used in industrial applications meet the necessary safety criteria, protecting workers and assets.
Conclusion:
Control cable standards are vital for ensuring efficiency, safety, and interoperability in industrial applications. By adhering to these standards, manufacturers can produce cables that meet the stringent requirements of control systems, withstand harsh operating conditions, and reduce the risk of electrical hazards. The impact of control cable standards extends to automation and control systems, industrial machinery, and workplace safety, enhancing overall productivity and mitigating potential risks. As technology continues to advance, control cable standards will continue to evolve, providing a solid foundation for the reliable and efficient operation of industrial processes.